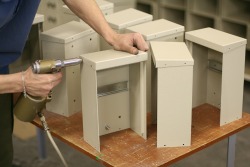
In his article on assembly time reduction, Mike Shipulski, a recognized leader in design engineering, calculates that "fasteners can consume 20-50% of assembly labor" time. Often overlooked or unassigned specifically to product cost as general overhead, the impact on the bottom line is palpable when you think about it in these cold hard numbers, which Shipulski likens to "death by a thousand cuts" to profitability.
While it's true that fasteners don't cost much individually, the cost adds up quickly when you calculate the number of fasteners used during an entire shift or for an entire project build. After you add the cost of labor, you end up with an expense that can benefit tremendously from proactive management. Shipulski also points out that, in a factory environment, fasteners actually impact floor space requirements: "...the number of assembly stations is proportional to demand times labor time. Since fasteners inflate labor time, they also inflate the number of assembly stations, which, in turn, inflates the factory floor space needed to meet demand."
There are several potential ways to avoid this and reduce assembly labor time. For instance, a portion of the build can be moved off-site, freeing up labor time to put toward other, less labor intensive tasks so production can proceed more rapidly. Handling subassembly off site can reduce end-product lead times, and end up becoming a lean manufacturing process that streamlines and improves operations.
Another way to reduce assembly time related to fasteners is to engineer a product so that it requires as few fasteners as possible, but such a design change is often out of the question if quality will be impacted.
So let's flip this around now and consider how fasteners can actually be a resource that facilitates the reduction of your assembly costs, improves your product quality and actually enhances your overall competitiveness. In fact, fasteners can be one of the high quality components that can improve assembly quality, extend product life, and reduce manufacturing or production costs.
We put the BECK Fastener Group®'s over 100 years of application engineering experience to this test, and the result was startling - production time can be significantly reduced by reengineering the simple fastener, making it faster to install without sacrificing quality.
The SCRAIL® Faster Fastener® is a performance-driven crossover combining a screw and a nail. These construction fasteners offer many advantages over the common nail or screw.
- Increased speed of application, which results in significant savings in labor costs.
- Driven by a pneumatic gun, they're twice as fast as the typical collated screw and eight times faster than manually installed bulk screws.
- They're designed and manufactured specifically for ease of use in most commercially available coil or strip nailers, so no new or custom equipment is required.
- Their unique configuration provides dramatically increased holding power when compared to the common screw or nail.
- Flexibility, since the thread configuration means they can easily be adjusted and/or quickly removed.
- Available in a wide range of specific configurations to optimize labor performance in applications such as drywall installation, framing, sub-flooring, decking, fencing, crate manufacturing, light gauge steel construction, furniture, and more.
To see SCRAIL® in action:
To learn more about industrial applications for SCRAIL® fasteners, you might enjoy reading our whitepaper, "Industrial Fasteners Must Withstand the Test of Time : Choosing the Right Fastener to Ensure Longevity in your Work."